Metalworking Solutions is a leader in sheet metal forming services, including bending material with our advanced press brake equipment. We also provide full-service metal fabrication, machining, welding, and finishing services.
Learn more about our press brake sheet metal bending services and equipment.
Press Brake Bending for Sheet Metal Fabrication
A press brake is an efficient and precise way to bend sheets or plates of metal. A sheet is placed between upper and lower dies. The upper die presses down on the metal to form the desired angle along the length of the workpiece. A piece called a back gauge then slides forward to hold the workpiece in position as it is bent. Machines are equipped with different tonnages that determine the force with which they press the material. The material used, thickness, and angle or shape to achieve all determine the appropriate tonnage.
Press brakes also have maximum lengths of material they can accommodate ranging from a few feet to 12 ft. or more. As a result, many metal fabricators operate several press brake machines in order to expand their capabilities.
Most modern press brakes are operated with hydraulics and CNC programming to repeat the same bends over and over for a high degree of repeatability and minimal variation. Bends of different angles and different effects are created with a variety of dies. Some common shapes and profiles include:
- Acute, obtuse, 90 degree angles
- U-bends and channels
- Corrugation
- Tubes and pipes
- Hemming (i.e., flat single or double fold)
Our Metal Bending Capabilities
At Metalworking Solutions capabilities include precision bending stainless steel sheet metal and other types and grades of sheet metal materials, up to ¾ in. thick and 14 ft. long. Additional capabilities include:
- Complex shapes and forms
- Tight tolerances, often within +/- 2 degrees
- Ejection of parts with special handling equipment
- Automated tool changing for efficiency
- Custom tooling to meet unique project needs
Exceptional Metal Bending Services with Cutting-Edge Press Brakes
We operate several press brakes of different tonnages and lengths, which allows us to fabricate the largest variety of sheet metal parts and components. Our experienced team excels at bending stainless steel sheet metal and other materials to meet customer requirements.
Amada HDS 2204 & HG 2204 Press Brake
These are 243 ton, 14 ft. press brakes, used for forming large parts. They can be used with sheet metals of various thicknesses and are equipped with AMNC 3i control technology, making it easy to use and ultra-precise. The newer HG 2204 provides the same functionality as the HDS plus additional forming capacity.
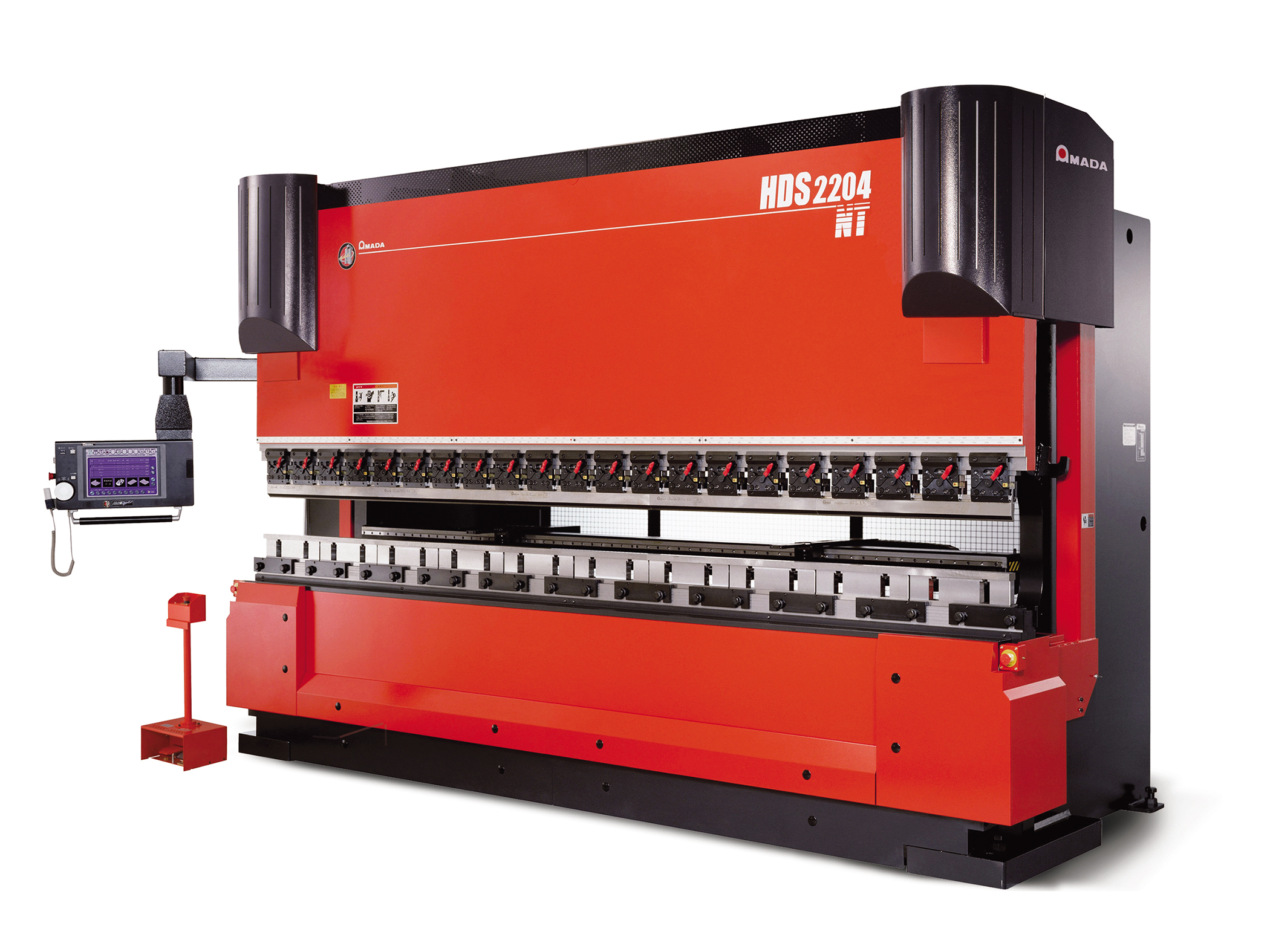
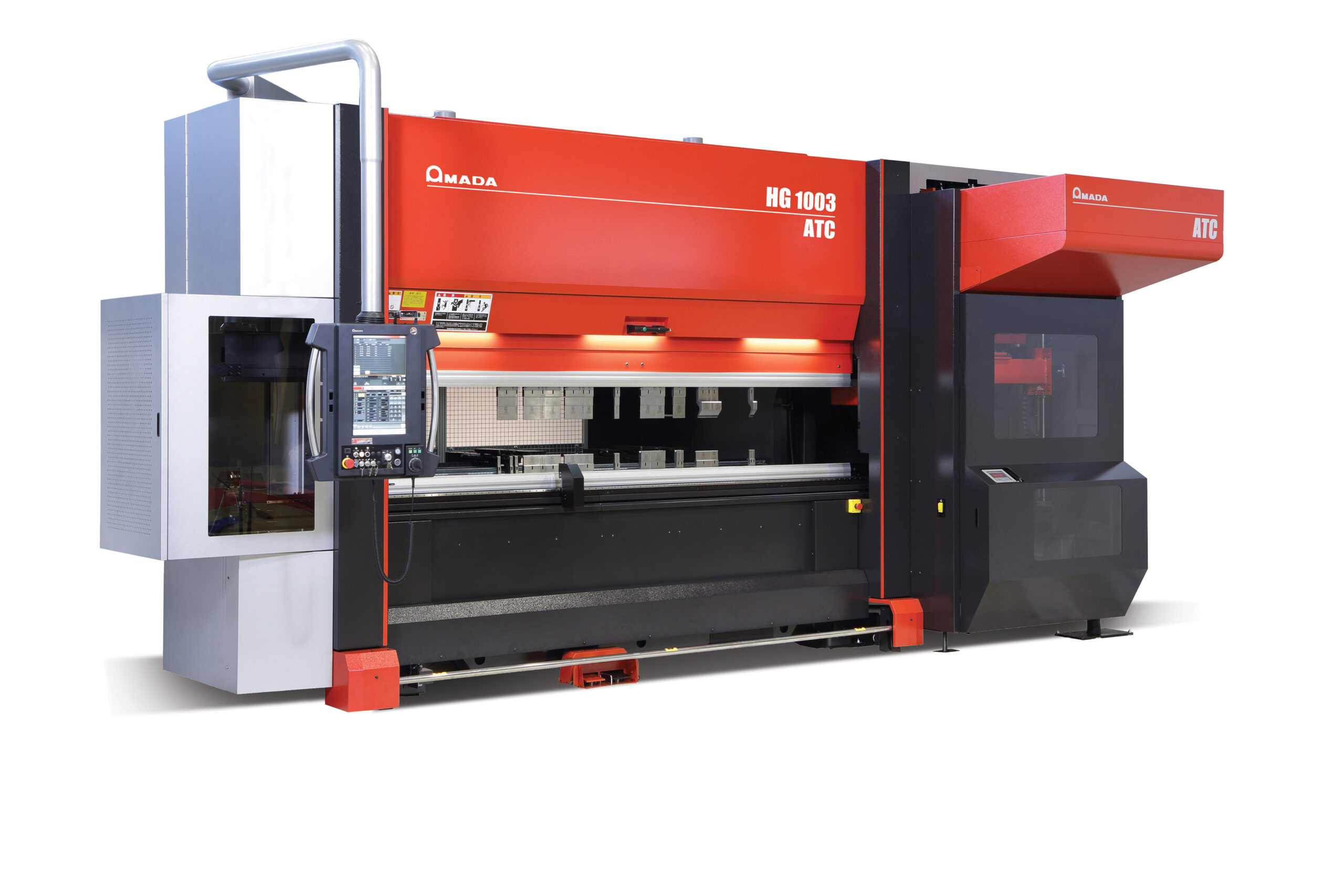
Amada HG 1003 ATC Press Brake
The HG 1003 is a 110 ton, 10 ft. press brake. It features an Automatic Tool Changer (ATC) system, and can store up to 86 ft. of tooling for fast changeover within three minutes. It is easily adjustable for complex designs and variable lot sizes.
Amada HG 1303 Press Brake
This is a midsize, 146 ton, 10 ft. press brake equipped with AMNC 3i controls. It is one of five press brakes this length in our facility.
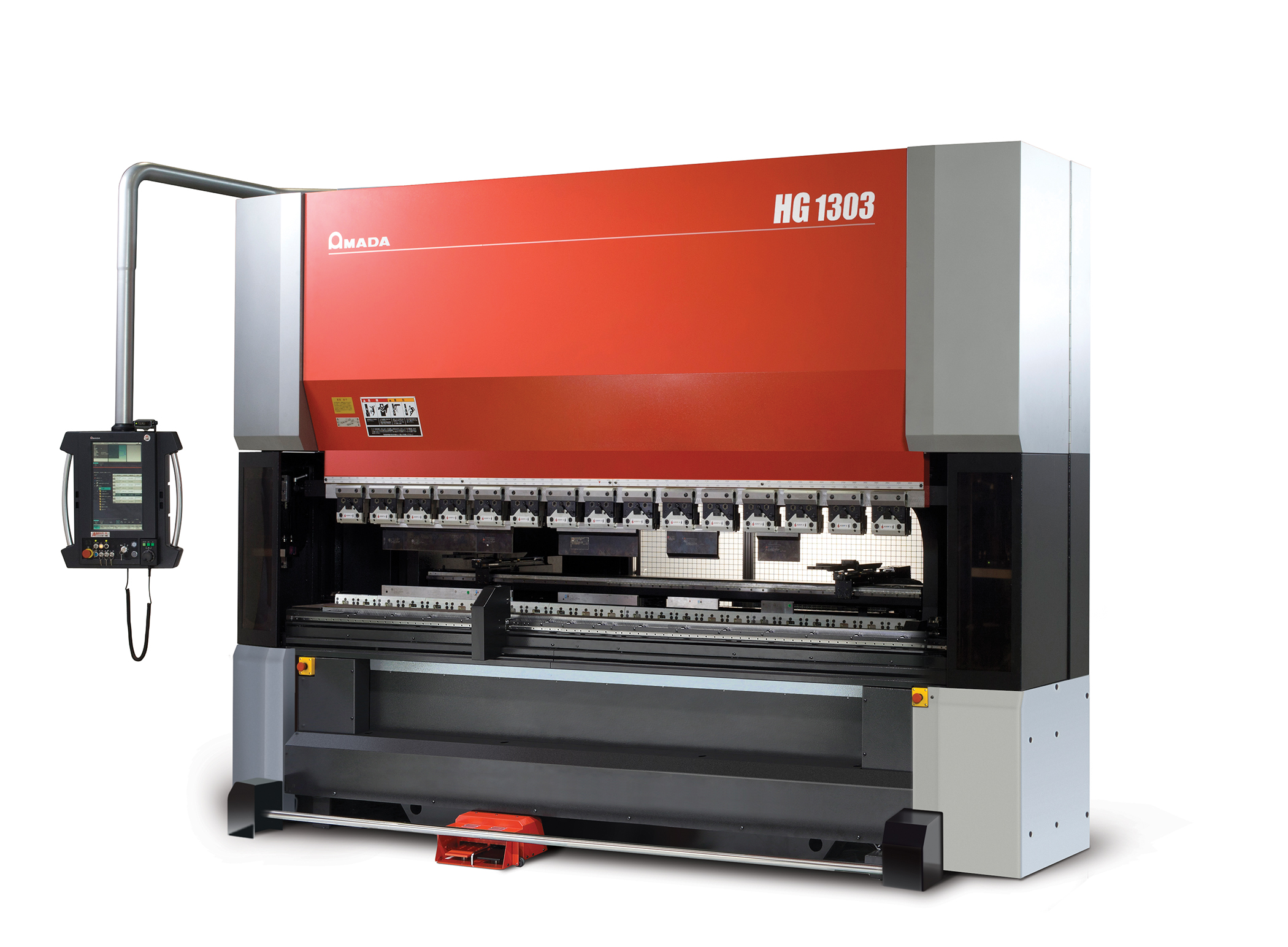
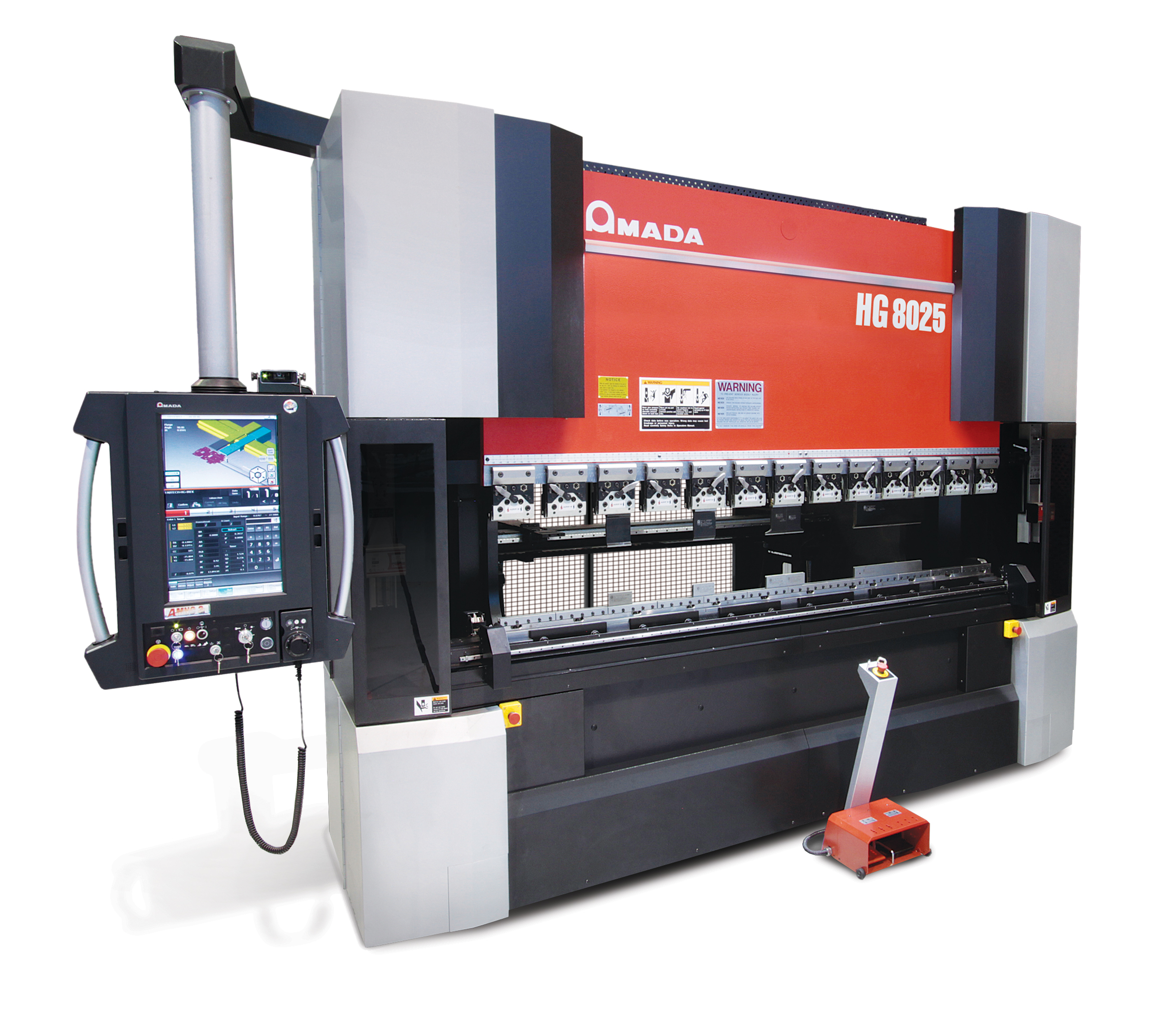
Amada HG 8025 Press Brake
The HG 8025 is a midsize, 89 ton machine with 102 in. length. It is fast and has a hybrid drive system for accuracy. It also features a smartphone-style 3D control unit.
Amada EG 6013 Press Brake
This 67 ton, 4 ft. press brake has a dual servo press (DSP) drive mechanism. It is a fast, ultra-precision machine that excels at forming small and complex parts.
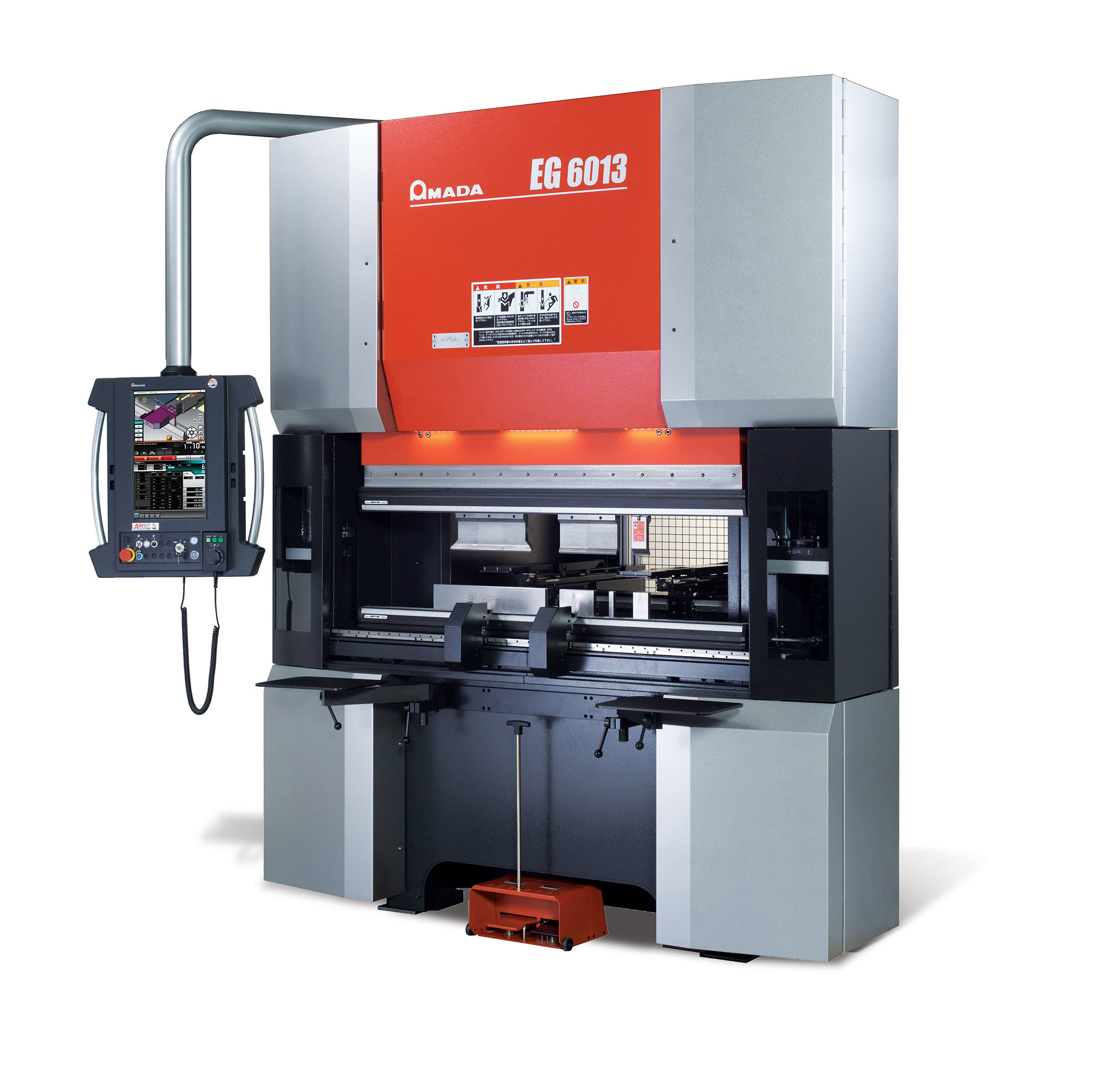
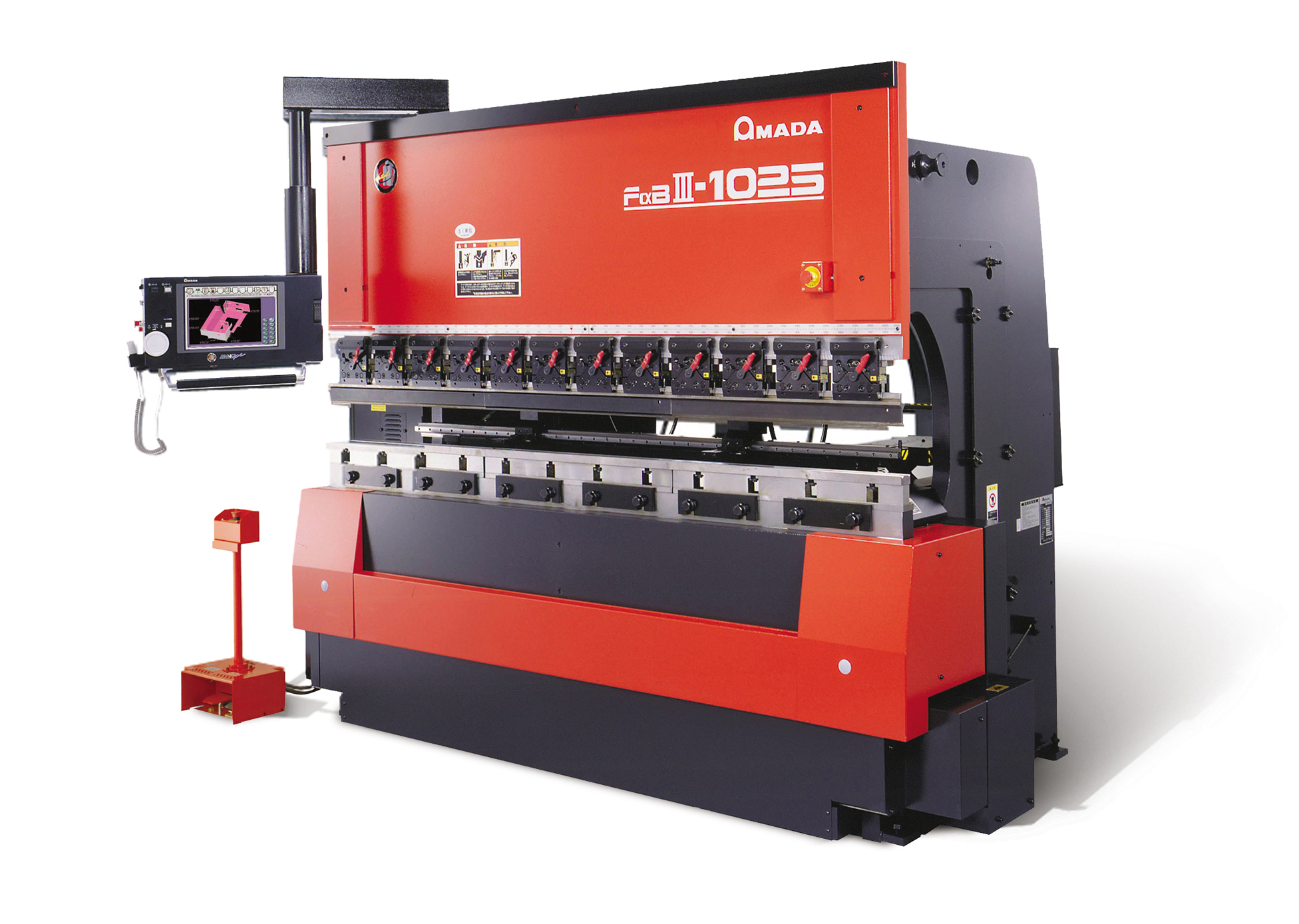
Amada 1025 Press Brake
We have two of this 110 ton, 10 ft. press brake model, which is powerful enough to work with most material thicknesses.
Amada RG M2 5020
Press Brake
Our two high-speed RGM2 series press brakes have a 35 ton capacity and 4 ft. length. It is used for small parts and features an increased processing speed and fast back gauge speed.
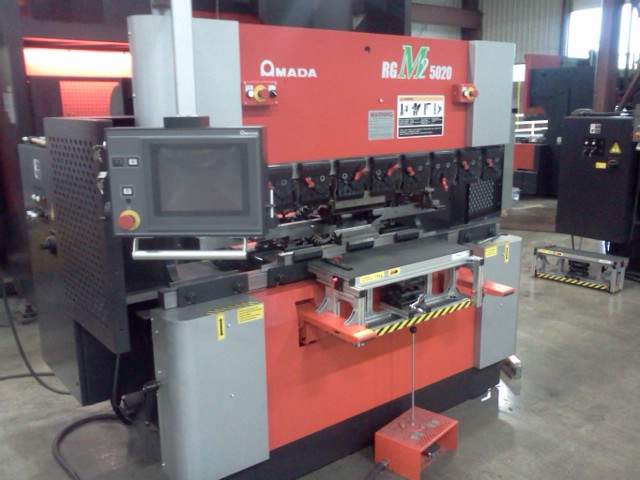
Choose Metalworking Solutions for Sheet Metal Fabrication
Metalworking Solutions is a one-stop partner for comprehensive metal fabrication services including metal cutting and bending services, turret punching, CNC machining, welding, finishing processes, and assembly. All projects include first article inspection for quality control and FabriVISION laser scanner technology for part validation.
Contact us to learn more about our sheet metal forming services, or to request a quote.